Hot Dip Galvanized vs GI Cable Trays: What’s the Difference?
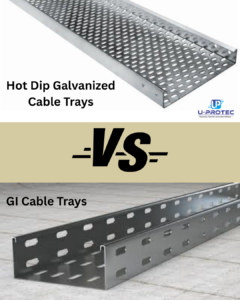
Cable Trays
When it comes to protecting electrical cables in commercial or industrial installations, choosing the right cable tray finish is critical. Two common types—Hot Dip Galvanized (HDG) and GI (Galvanized Iron) cable trays—offer corrosion protection but differ significantly in performance, durability, and application.
In this post, we’ll explore the key differences between Hot Dip Galvanized vs GI cable trays, helping you decide which is right for your project.
What is a GI Cable Tray?
GI cable trays are made from galvanized iron, typically manufactured using pre-galvanized steel sheets. The zinc coating is applied before the fabrication process.
Key Features:
- Uniform zinc coating from factory
- Economical and lightweight
- Suitable for indoor applications
- Limited corrosion resistance in outdoor or humid environments
What is a Hot Dip Galvanized (HDG) Cable Tray?
Hot dip galvanized cable trays are made from steel and then immersed in molten zinc after fabrication. This post-fabrication process ensures complete coverage.
Key Features:
- Thicker and more robust zinc coating
- Better protection for edges, welds, and holes
- Ideal for harsh environments
- Long-lasting corrosion resistance
Hot Dip Galvanized vs GI Cable Trays: Comparison Table
Feature | GI Cable Trays | Hot Dip Galvanized (HDG) Cable Trays |
Coating Process | Pre-galvanized (before fabrication) | Hot dip galvanized (after fabrication) |
Zinc Coating Thickness | 80–120 gsm (grams per sq. meter) | 300–600 gsm |
Corrosion Resistance | Moderate | High |
Best Use Case | Indoor/dry locations | Outdoor, coastal, or industrial environments |
Cost | Lower initial cost | Slightly higher, better long-term value |
Edge/Weld Protection | Exposed metal may corrode | Fully coated, even at cut edges and welds |
Durability | Less durable in harsh conditions | Highly durable over decades |
When to Use GI Cable Trays
Choose GI cable trays when:
- Your project is indoors, such as office spaces or retail stores
- The environment is dry with minimal exposure to moisture or chemicals
- You’re working with a tight budget
Note: While GI trays offer cost savings, they may degrade faster in damp or corrosive areas.
When to Use Hot Dip Galvanized Cable Trays
Choose HDG cable trays when:
- Your installation is outdoor, coastal, or exposed to high humidity
- You require long-term durability and minimal maintenance
- You’re working in industrial environments, such as chemical plants or factories
Which One Should You Choose?
Here’s a quick decision guide:
- ✅ Choose GI Cable Trays for: Low-cost indoor installations
- ✅ Choose Hot Dip Galvanized Cable Trays for: Outdoor or harsh industrial environments
Even though HDG trays have a higher upfront cost, they often provide better long-term value due to their extended lifespan and reduced maintenance needs.
Compliance and Standards
When selecting cable trays, ensure compliance with relevant standards:
- IS 2629 and IS 4759 (for hot dip galvanizing)
- IEC 61537 (international standard for cable trays)
- NEMA VE 1 (for metal cable tray systems)
Final Thoughts
Understanding the difference between Hot Dip Galvanized vs GI cable trays is essential for safe, reliable, and cost-effective electrical installations. While GI trays suit indoor environments, HDG trays are the go-to solution for corrosion-prone, outdoor, and industrial settings.
Need help choosing the right tray for your project? Consult a certified electrical engineer or a cable tray manufacturer for guidance based on your specific requirements.
FAQs
Q1: Is HDG better than GI for all applications?
A: Not necessarily. HDG is better for corrosion resistance, but GI is more cost-effective for dry indoor environments.
Q2: Can I use GI cable trays outdoors?
A: It’s not recommended. They may corrode quickly unless used in mild, dry climates.
Q3: How long does a hot dip galvanized tray last?
A: With proper installation, HDG trays can last 20–40 years depending on environmental exposure.